Taking the Pressure Off with Central Tyre Inflations Systems
22 April 2024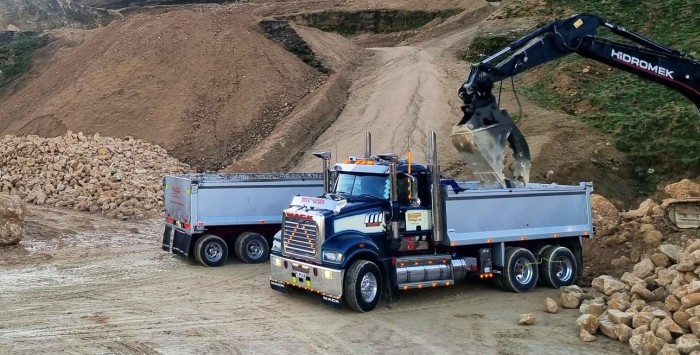
By New Zealand Truckbody & Trailer Magazine
It seems that every year the level of automation and computer control of different truck systems increases. Features like lane adaptive cruise control, automatic emergency braking, lane assist and blind spot monitoring are rapidly moving from the advanced features list to standard equipment – but there is one feature that is likely to remain on the accessory list for a while at least, and that is central tyre inflation systems.
While more people are starting to understand that tyre pressure is the most important factor in tyre performance and tyre life, the usual requirement is to maintain tyres at the recommended pressure for the road.
In Europe and America, the vast majority of heavy transport miles occur on tarmac so, while more vehicle manufacturers are including tyre pressure monitoring, there is as yet little demand there for systems that will deliver pressure adjustment on the fly. To some extent, too, manufacturers look at tyres as consumables which are squarely in the operators’ sandbox to manage.
The picture is different in New Zealand. The ability to raise and lower tyre pressures is a practical requirement here where so many heavy transport vehicles operate both on-road and offroad, particularly in forestry but also in agriculture.
Being able to lower tyre pressures for added traction on muddy forest skids and access roads in winter – and on farms – and quickly reinflate them for open road speeds is a real boon, so there is a thriving aftermarket here in central tyre inflation systems.
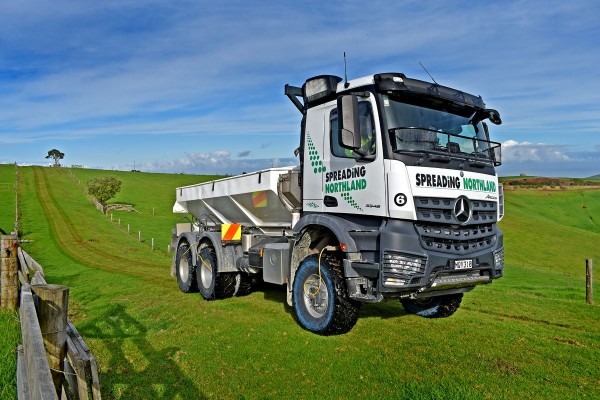
Fitting CTI to steerers as well as drive wheels ensures Spreading Northland can keep moving in the right direction
Saving time, tyres and tankers
In the past drivers have taken compressors with them into the forest but it was still time-consuming, first deflating drive tyres then getting around them all again with an airline from the compressor. And doing so was always more likely to be needed in wet or muddy conditions. Having a system that deflates and reinflates tyres accurately, which is operated and controlled from the comfort of the cab, offering real productivity gains to drivers – but not just to individual truckies.
A vehicle stuck on an access road or a loading skid in a forest will immediately hold up everyone trying to work on that site. Some clever people have calculated trucks with tyre pressures lowered to around 32 psi achieve around a 30 per cent improvement in getting the torque down. Giving drivers that much more confidence that they can handle bad conditions has also got to reduce their stress levels overall.
Manager of one of the most popular systems, Traction Air’s Grant Ferguson, says nowadays many forest owners or operators won’t allow trucks into some areas without a tyre pressure control system. It’s seen as an essential safeguard against delays. Nor do they want to have to repair the inevitable damage caused by a stuck vehicle and the manoeuvres required to free it again.
Grant says it’s not just logging trucks that get the system fitted. Traction Air is being fitted to more and more tractors and trucks involved in harvesting on farms.
“Also power company vehicles that have to service facilities in remote areas, and fuel trucks, which can also be transporting heavy loads into remote areas.”
Unlike with logging trucks, there’s a lot of rigid superstructure in a tanker body so reducing tyre pressures on rough roads also reduces vibration and stresses transmitted to the bodies, reducing wear and tear and maintenance costs. There’s a big difference, too, in fuel tankers’ laden and unladen weights, so even for use on the road there are gains to be made in tyre life, truck handling and therefore safety.
There’s growth too in vehicles involved in civil construction.
“Particularly after Cyclone Gabrielle in Hawke’s Bay, we got a lot of orders from people who wouldn’t be able to operate otherwise,” Grant says.
Sooty Breach, managing director of Paraparaumu-based Clive Taylor Haulage Ltd, did exactly that for the Mack sent to Hawke’s Bay to help with the clean up. Sooty hadn’t used CTI before; it wasn’t around in the days when he was driving logging trucks but thought he would “give it a go”.
“The operator of that truck definitely noticed the difference, especially when it’s empty, if he has to get out of some tricky spots. He can get out of it quite nicely instead of having to be a bit more aggressive and hit it at speed.”
Sooty says his experience so far convinced him to also fit it to a nine-axle HPMV vehicle in build at the moment. Even after the Gabrielle work, they will be working offroad in quarries and on farms and the extra traction will always be welcome.
Multiple choice
Grant says most systems can be programmed with four settings catering for loaded and unloaded conditions, both on-road and off road.
While there maybe some gains in having the system fitted to steerers, the biggest gains and increasing the traction of drive wheels, so most installations restrict themselves to those axles.
4x4 vehicles or 8x8s can have a single channel system fitted which sets the pressures on the front drive axles to the same as the rear, or a two-channel system that allows different pressures between front and rear axles.
The head units also have the capability to run a third channel if required so the system could set different pressures for drive wheels, steerers and trailer axles. “We can pretty much plumb in anything.”
As with everything else, the degree of control and automation only gets more sophisticated. Grant says early displays were quite basic but Traction Air’s displays have been updated to be easier to read and use. There’s the choice of an industry first touch screen head unit which can be bracket mounted, flush mounted or there’s a pushbutton version to fit a spare DIN slot in the dash.
Adding in GPS information has provided more features. It advises the control unit of the vehicle’s speed, so if a logging truck accelerates to highway speeds after coming out of the forest and the driver has not reinflated the tyres to suit highway speeds the head unit in the cab will sound an alert. Some systems can use that signal to reinflate automatically, as a safety feature.
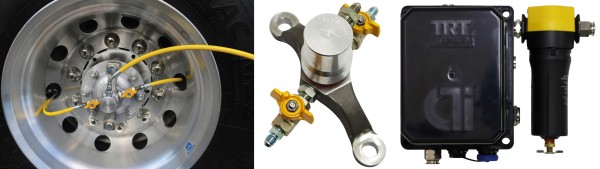
From left to right: Traction Air’s distinctive yellow lines, the hub-mounted rotator unit and the new sealed composite pressure cell, which is about 50 percent smaller than the previous model
In addition, TRT’s Traction Air system will detect a puncture. The system will notice the drop in pressure or the extra demand on the air pump and an alarm will alert the driver. If the leak is not catastrophic, it could also maintain tyre pressure until it is safe to change the wheel. Pressures are displayed in real time.
Not everything can be left to the system, though. Grant says the Traction Air system is an open system, which means all wheels on a channel are pressurised by a common feed. That means the taps on individual wheels should be turned off each night as a puncture picked up at the last minute – or left unattended – could see the whole lot flat in the morning, instead of just one. The system will also alert the driver to turn the taps back on again the next day.
Continuous improvement
The design of TRT’s Traction Air system has evolved and improved over time. TRT released a new system, the EM series, in November last year. One of the biggest advantages of the new system is that it is smaller. The pressure cell, the compressor and distribution unit, is about 50 percent smaller than the previous model.
“Traction Air is often the last accessory to be added to a truck and finding the right location for them can be tricky. Making it smaller gives us a lot more options,” says Grant.
It features an entirely new moulded manifold design that optimises airflow and pressure equalisation. It also significantly reduces the complexity, weight and the number of parts and components compared with the older model. Even though the old model was reliable, there’s much less potential for failure, and the composite cover, sealed to IP66, enhances environmental protection for the system.
The head unit is also future-proofed having additional inputs and outputs for integration with CANBUS.
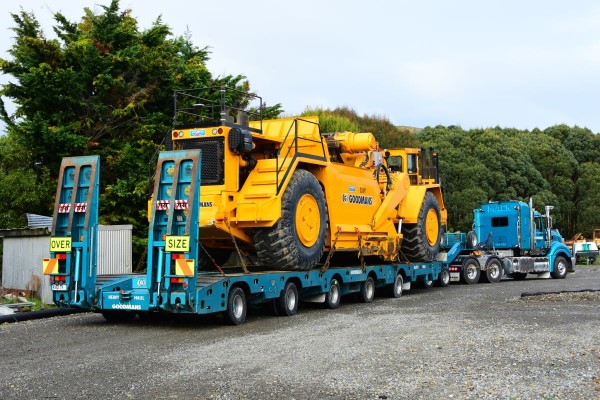
Goodman Contracting’s Mack Titan heavy hauler
Most people would be able to spot a TRT Traction Air equipped truck, the telltale clue being the presence of a yellow armoured airline snaking around the guards of the drive wheels to a ‘rotator’ fastened to the wheel hub. Secondary lines from the rotator connect to the valves of each tyre on that end of the axle. The rotator is the key bit of kit in the system.
The free-spinning cap (or rather a spinning body under a stationary cap) allows a pressurised feed from a fixed line to supply the dual tyre valves that are rotating at wheel speed while keeping all the air in. That’s not always the case though. Lines can be fed through the axle for a variety of different trailer fitments. Traction Air has options for most leading market brands: ROR, BPW and SAF for example.
Traction Air claims to have the most durable rotator on the market. Its Compact model wheel end rotator has tungsten carbide and carbon seal facings to deliver maximum strength and durability.
Traction Air also offers a heavy-duty high-temperature hub reduction rotator, developed specifically for dealing with the heat generated by hub reduction vehicles operating in Australia’s blistering mid-summer temperatures. Grant says the finned design carries heat away from the internal seal facings, significantly improving operational life.
Traction Air dates back to 1997 when TRT’s managing director, Bruce Carden, took notice of the Redline product which was already well established in the Canadian logging industry. He saw an opportunity to locally manufacture a more affordable and hopefully improved alternative to Redline.
TRT’s first Traction Air system was fitted to a Trevor Masters Kenworth logging truck in March 1997.
TRT followed up, fitting its first Traction Air system in Australia in 1999 for Ken Padgent, who operated out of Scottsdale, Tasmania.
The fully loaded B-double weighed over 60 tonnes and had to start on a gravel haul road with roughly a 15 percent gradient.
“It had no trouble pulling away from there,” Ken remarked. The drive tyres set at 32 psi provided so much traction that the front axle lifted off the road.
Traction Air was also installed on the world’s first triple road train, which was operating out of Alice Springs. This rig had Traction Air systems on all 96 tyres. The Tanami Desert Road is harsh, and the ability to reduce tyre pressure resulted in substantial maintenance savings for Australian Fuel Distributors.
In March 2009, Traction Air launched the G Series, featuring GPS ‘speed up control’ and dual transducer sensing for world leading accuracy. In September 2019, TRT introduced the Traction Air E-Series in Australia and New Zealand, the precursor to the current EM series.
Bruce Carden says, “As with all our TRT manufactured products, Traction Air has made significant strides in terms of design, capability, and functionality. The new Traction Air EM Series is yet another example demonstrating our commitment to delivering the best possible solutions for our valued customers.”
Traction Air has been fitted to more than 4000 vehicles across Australia and New Zealand. It has has also been distributed in Sweden and across Asia.
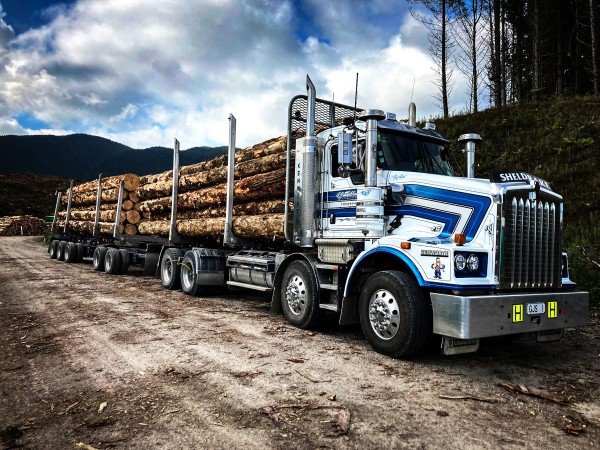
32 wheels but Traction Air on just eight of them gets the job done